Gears are everywhere—from bicycles and clocks to cars and industrial machines. They play a fundamental role in mechanical systems, allowing power transmission, torque adjustment, and speed regulation. A gear is a rotating circular machine part with teeth (cogs) that interlock with another gear to transfer motion and force.
But how exactly do gears work? Why are there so many different types? And why are they so widely used in mechanical engineering, automotive systems, and industrial machinery? This complete guide will cover everything you need to know about gears, including their working principles, key parts, different types, advantages, disadvantages, and practical applications.
What Is a Gear?
A gear is a mechanical component designed to transmit power between two rotating shafts. It consists of teeth (cogs) evenly spaced around a circular surface, allowing precise motion control.
Gears are used to change speed, increase or decrease torque, and reverse rotational direction. They are a key element in gearboxes, transmissions, and industrial power systems.
In simple terms, gears function as force multipliers, making machines more efficient and adaptable for various applications.
How Do Gears Work?
Gears operate based on interlocking teeth that transfer rotational motion from one gear to another. Their working principle involves:
- Meshing Mechanism – When two gears engage, their teeth interlock, ensuring synchronized movement.
- Speed Control – The gear with fewer teeth rotates faster, while the larger gear rotates slower but delivers higher torque.
- Torque Transmission – A smaller gear (pinion) can drive a larger gear to increase force output, making it ideal for heavy machinery.
- Direction Change – Some gear arrangements reverse rotational direction, used in steering systems and mechanical linkages.
By adjusting gear ratios, engineers can fine-tune speed, efficiency, and mechanical power output in different systems.
Why Use Gears?
Gears are essential in mechanical systems due to their ability to:
- Modify Speed & Torque – Gears help in increasing or decreasing speed and force, ensuring the right power is delivered to the output.
- Enable Precise Motion Control – Gears ensure accurate and repeatable motion, making them indispensable in robotics, clocks, and machinery.
- Improve Mechanical Efficiency – They reduce energy loss in power transmission, making systems more fuel-efficient and reliable.
- Reverse Rotational Direction – Certain gear arrangements change the motion direction, useful in automotive steering and industrial applications.
Without gears, many modern machines, vehicles, and industrial processes would not function efficiently.
Parts of a Gear
Each gear consists of several crucial components that determine its performance and functionality:
1. Axis
The axis is the central point around which the gear rotates. It provides a stable connection to the shaft or transmission system.
2. Teeth
Gears have precisely cut teeth (cogs) that interlock with another gear to ensure synchronized motion transfer.
3. Pitch Circle
The pitch circle is the imaginary circle where two gears make contact, defining the effective point of engagement.
4. Pitch Diameter
The pitch diameter is the distance across the pitch circle, affecting gear speed and torque.
5. Diametral Pitch
This represents the number of gear teeth per inch of pitch diameter, influencing gear precision and power output.
6. Circular Pitch
The circular pitch is the distance between teeth, ensuring consistent spacing for smooth engagement.
7. Module
The module is the gear’s size measurement, determining compatibility with other gears in a system.
8. Pressure Angle
The pressure angle influences how force is transferred between gears, affecting load distribution and efficiency.
Each of these parts plays a crucial role in gear performance, making them vital for mechanical precision and efficiency.
Types of Gears
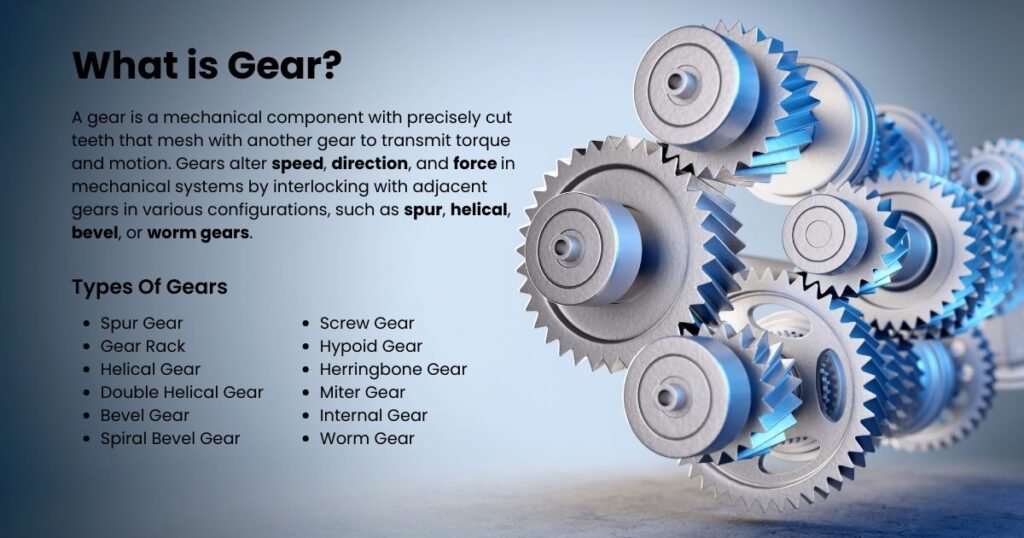
Gears come in various shapes, sizes, and configurations, each suited for specific mechanical functions. Below are the most commonly used gear types:
1. Spur Gear
A spur gear is the simplest and most common type, featuring straight teeth parallel to the gear axis.
- Used in: Clocks, washing machines, industrial conveyors
- Advantage: High efficiency and easy manufacturing
2. Gear Rack
A gear rack is a linear gear that meshes with a circular pinion gear to convert rotary motion into linear movement.
- Used in: Steering systems, CNC machines, elevators
- Advantage: Provides precise linear motion control
3. Helical Gear
A helical gear has angled teeth, allowing smoother and quieter power transmission.
- Used in: Automotive transmissions, turbines, industrial presses
- Advantage: Reduces noise and distributes load evenly
4. Double Helical Gear
A double helical gear features two helical rows in opposite directions, eliminating axial thrust.
- Used in: High-speed ships, turbines, mining equipment
- Advantage: Increases load capacity and durability
5. Bevel Gear
A bevel gear features cone-shaped teeth, allowing power transfer between intersecting shafts.
- Used in: Automobiles, drills, locomotives
- Advantage: Enables smooth right-angle motion transfer
6. Spiral Bevel Gear
A spiral bevel gear has curved teeth, offering gradual engagement and improved load handling.
- Used in: High-speed transmissions, helicopters, differential systems
- Advantage: Reduces vibration and impact stress
7. Screw Gear
A screw gear operates at non-parallel, non-intersecting shafts, useful for low-speed torque applications.
- Used in: Industrial mixers, robotics
- Advantage: Allows silent and precise operation
8. Hypoid Gear
A hypoid gear has offset shafts, allowing higher torque transmission than bevel gears.
- Used in: Vehicle differentials, industrial drives
- Advantage: Improves torque efficiency and load distribution
9. Herringbone Gear
Similar to double helical gears, but with continuous teeth alignment, enhancing efficiency.
- Used in: Heavy-duty machinery, oil rigs
- Advantage: Handles high torque loads without vibrations
10. Miter Gear
A miter gear transmits equal torque between two intersecting shafts at a 90° angle.
- Used in: Robotics, woodworking machines
- Advantage: Provides smooth, efficient motion control
11. Internal Gear
An internal gear has teeth cut on the inside surface, allowing compact gear arrangements.
- Used in: Planetary gear systems, mechanical clocks
- Advantage: Provides space-efficient power transmission
Each gear type serves a unique function, offering specialized benefits for different mechanical and industrial applications.
12. Worm Gear
A worm gear consists of a worm screw and a worm wheel, delivering high torque at low speeds.
- Used in: Elevators, conveyor belts, security gates
- Advantage: Ensures self-locking mechanism for added safety
Advantages of Gears
Gears are widely used in mechanical systems due to their efficiency, durability, and precise motion control. Here are the key benefits of using gears:
1. High Power Transmission Efficiency
Gears provide efficient power transfer between rotating shafts, ensuring minimal energy loss. Compared to belts and chains, gears deliver consistent motion with higher accuracy.
2. Speed and Torque Regulation
By adjusting gear ratios, gears help increase or decrease speed and torque. Larger gears reduce speed but increase torque, while smaller gears increase speed but reduce torque.
3. Precise Motion Control
Gears offer precise synchronization, making them ideal for industrial automation, clocks, and robotics. Their tooth engagement ensures exact movement, improving accuracy in machines.
4. Long-Lasting Durability
Made from high-strength materials, gears are resistant to wear and tear, ensuring long-term reliability in harsh conditions.
5. Reversibility of Motion
Certain gear arrangements can change rotational direction, making them essential for steering systems and reversing mechanisms.
6. Compact and Space-Efficient Design
Compared to belt and chain drives, gears occupy less space while delivering the same or even better power output.
Disadvantages of Gears
While gears offer many advantages, they also have some limitations:
1. Noise and Vibration
Improper gear meshing or worn-out teeth can cause excessive noise and vibrations, affecting machine performance.
2. Complex Manufacturing Process
Gears require precision machining, making them costlier to manufacture than simpler transmission systems.
3. Lubrication Requirements
To prevent friction and overheating, gears need regular lubrication and proper maintenance.
4. Higher Initial Costs
High-quality gears, especially spiral bevel and hypoid gears, have a higher upfront cost due to their complex design.
Despite these drawbacks, proper maintenance and selection of the right gear type can minimize these issues, ensuring efficient operation.
Applications of Gears
Gears are used across multiple industries, offering versatility and reliability in power transmission and motion control. Below are some key industries that rely on gears:
1. Automotive Industry
Gears play a vital role in vehicle transmissions, steering systems, and engine components.
- Manual & automatic transmissions use spur, helical, and planetary gears.
- Differential gears balance wheel speed for smoother turning.
- Worm gears help in power steering systems.
2. Industrial Machinery
Gears drive heavy-duty industrial machines, ensuring precise movement and power distribution.
- Helical gears are used in printing presses and textile machines.
- Worm gears operate conveyors and elevators.
- Spiral bevel gears power steel mills and mining equipment.
3. Aerospace Industry
Aircraft use high-precision gears for landing gear, navigation, and propulsion systems.
- Hypoid and bevel gears handle flight control mechanisms.
- Planetary gears operate jet engine turbines.
4. Marine and Shipbuilding
Ships rely on gear systems for propulsion and navigation.
- Bevel and herringbone gears drive marine propellers.
- Right-angle gears are used in rudder control systems.
5. Robotics and Automation
Gears enable accurate movement and control in automated systems.
- Planetary gears drive robotic arms.
- Rack and pinion gears provide linear motion in CNC machines.
6. Renewable Energy
Wind and hydroelectric plants rely on gearboxes to optimize power generation.
- Planetary gearboxes are used in wind turbines.
- Helical gears regulate hydroelectric generators.
Gears are an essential part of modern technology, ensuring efficiency, precision, and reliability across various industries.
How to Maintain Gears for Long-Term Performance?
Proper maintenance and servicing can significantly extend the lifespan of gears, ensuring efficient operation and preventing breakdowns.
1. Lubrication and Oil Changes
- Gears need adequate lubrication to minimize friction and wear.
- Regular oil changes prevent contaminant buildup, improving gear efficiency.
2. Routine Inspections
- Check for worn-out teeth, misalignment, and excessive vibration.
- Inspect gear backlash to ensure proper engagement.
3. Temperature Monitoring
- Overheating gears can cause premature wear. Ensure proper cooling mechanisms are in place.
4. Avoid Overloading
- Exceeding the designed torque capacity leads to gear failure. Always operate within recommended load limits.
A well-maintained gear system ensures longevity, reducing operational costs and increasing efficiency.
Conclusion
Gears are one of the most fundamental components in mechanical engineering, ensuring smooth motion control, power transmission, and operational efficiency. From automobiles and industrial machines to aerospace and robotics, gears enable precision and performance in countless applications.
Understanding how gears work, their different types, advantages, and maintenance requirements helps in choosing the right gear system for any mechanical need. Whether in high-speed engines, precision robotics, or heavy-duty industrial machinery, gears remain an essential part of modern mechanical systems.
FAQs
What is the primary function of a gear?
A gear is used to transfer motion and power between rotating shafts. It can increase or decrease speed, modify torque, and reverse rotational direction.
How do I know if my gears need replacement?
Signs of worn-out gears include grinding noises, irregular movement, excessive heat, and poor power transmission. Regular inspections and lubrication can help prevent failure.
What is the difference between a helical gear and a spur gear?
A spur gear has straight teeth, making it noisy at high speeds, while a helical gear has angled teeth, reducing noise and improving load distribution.
Can gears work without lubrication?
No, gears require lubrication to prevent friction, overheating, and premature wear. Dry-running gears will fail quickly.
Are gears used in electric vehicles (EVs)?
Yes, electric vehicles use gear reduction systems, typically single-speed planetary gear sets, to optimize torque and power output.
Which gear type is best for high-load applications?
For high-load applications, helical, planetary, and herringbone gears provide superior strength and efficiency.