The camshaft is a fundamental component in an internal combustion engine that controls the operation of intake and exhaust valves. This rotating shaft features carefully designed lobes that push against valve lifters to open and close valves with precise timing. Without a properly functioning camshaft, your engine would fail to breathe correctly, severely affecting performance, fuel efficiency, and overall reliability.
For anyone who owns a vehicle or has an interest in how engines work, understanding camshafts provides valuable insight into engine operation and maintenance. In this comprehensive guide, we’ll explore everything from basic camshaft functions to advanced topics like camshaft position sensors, helping you grasp this critical engine component.
What is a Camshaft?
A camshaft is a rotating shaft used in piston engines to operate valves. It consists of a cylindrical rod running through the engine with a series of cams (lobes) that convert rotational motion into linear motion. These carefully shaped lobes push against valve lifters as the camshaft rotates, precisely opening and closing intake and exhaust valves.
Camshafts are typically made from hardened steel or cast iron to withstand the continuous stress they experience. The design of each lobe determines how far a valve opens, how long it stays open, and how quickly it closes. These characteristics, known as valve lift, duration, and timing, directly influence engine performance characteristics.
Most modern passenger vehicles use overhead camshaft designs where the camshaft is positioned above the cylinder head. This arrangement reduces mechanical complexity compared to older pushrod designs and allows for more precise valve control. Depending on the engine configuration, you might find a single camshaft operating both intake and exhaust valves, or separate camshafts for each set of valves in dual overhead camshaft (DOHC) arrangements.
How Does a Camshaft Work?
The camshaft operates through a synchronized relationship with the crankshaft, typically rotating at half the crankshaft speed in four-stroke engines. This relationship ensures valves open and close at the correct time during the engine’s intake, compression, power, and exhaust strokes.
As the camshaft rotates, each lobe pushes against a valve lifter, follower, or rocker arm. When the highest point (nose) of the lobe contacts the follower, the valve opens fully. As the lobe rotates away, a spring returns the valve to its closed position. This continuous cycle happens thousands of times per minute in a running engine.
The timing of this operation is critical. Intake valves must open when the piston moves downward on the intake stroke to draw in air and fuel. Similarly, exhaust valves must open when the piston pushes upward on the exhaust stroke to expel spent gases. The camshaft ensures this synchronization through its connection to the crankshaft via a timing belt, chain, or gears.
Modern engines often employ variable valve timing (VVT) systems that can adjust camshaft timing while the engine runs. This technology improves performance across different engine speeds by optimizing valve operation for changing conditions. Some advanced designs even vary valve lift and duration, further enhancing efficiency and power.
Camshaft Location in Different Engine Designs
Camshafts can be positioned in several locations depending on the engine design, each with specific advantages and characteristics. Understanding these configurations helps clarify how different engines operate.
In overhead valve (OHV) engines, also known as pushrod engines, the camshaft sits within the engine block. This design uses pushrods and rocker arms to transfer motion from the camshaft to valves in the cylinder head. While this arrangement creates a compact engine with a lower center of gravity, it typically limits engine speed due to the added moving parts.
Overhead camshaft (OHC) designs position the camshaft directly above the valves in the cylinder head. Single overhead camshaft (SOHC) engines use one camshaft to operate both intake and exhaust valves, often through rocker arms. This setup reduces mechanical complexity compared to pushrod designs and allows for higher engine speeds.
Dual overhead camshaft (DOHC) engines feature separate camshafts for intake and exhaust valves. This configuration enables more precise valve control and often allows for more valves per cylinder, improving airflow and engine efficiency. Most modern high-performance engines use DOHC designs for these benefits.
Some specialized engines employ even more complex arrangements, such as quad-cam designs with four camshafts or engines with camshafts positioned between cylinder banks in V-configuration engines.
Types of Camshafts
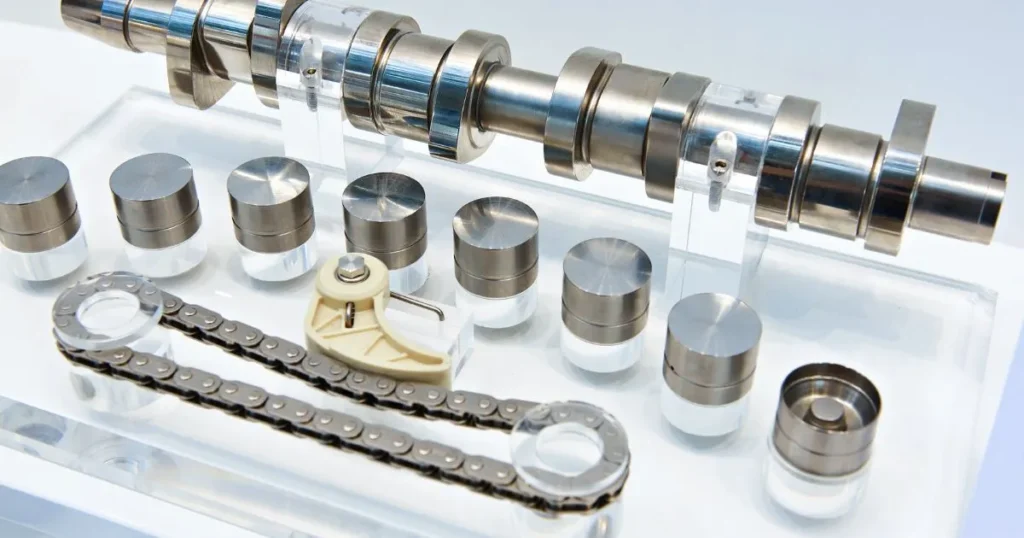
Camshafts come in various designs, each optimized for specific performance characteristics. The differences primarily relate to lobe profile, material composition, and manufacturing methods.
Stock camshafts
Stock camshafts are designed for balanced performance, emphasizing reliability, fuel efficiency, and moderate power. These camshafts typically provide smooth idle quality and good low to mid-range torque, making them ideal for everyday driving.
Performance camshafts
Performance camshafts feature more aggressive lobe profiles with increased lift and duration. These modifications allow more air and fuel into the cylinders and keep valves open longer, generating more power at higher engine speeds. However, this often comes at the expense of low-end torque and fuel economy.
Racing camshafts
Racing camshafts take performance characteristics to extremes, with very high lift and long duration. These specialized camshafts are designed for competition where maximum power at high RPM is the priority, often sacrificing drivability and efficiency.
Material choices also differentiate camshafts. While most production engines use cast iron or hardened steel camshafts, some high-performance applications employ billet steel, which offers superior strength. The manufacturing process also varies, with some camshafts being cast and others machined from solid stock (billet) for more precise specifications.
What is a Camshaft Position Sensor?
A camshaft position sensor is an electronic device that monitors the rotation and position of the camshaft. This sensor provides vital data to the engine control module (ECM) about valve timing, which the ECM uses to coordinate fuel injection and ignition timing.
The sensor works by detecting a reference point on the camshaft, often a notch or a series of teeth on a reluctor wheel. As these reference points pass by the sensor, they generate electrical signals that the ECM interprets to determine the exact position of the camshaft in relation to the crankshaft.
This precise timing information is crucial for modern fuel-injected engines, especially those with variable valve timing systems. Without accurate camshaft position data, the engine computer cannot properly time fuel injection or spark events, leading to poor performance, reduced fuel economy, and increased emissions.
Camshaft position sensors typically use one of three technologies: magnetic (Hall effect), optical, or reluctance. Hall effect sensors are most common, using changes in magnetic fields to generate signals as the camshaft rotates. These sensors offer good reliability and accuracy in the harsh engine environment.
Symptoms of a Bad Camshaft Position Sensor
A failing camshaft position sensor can cause various problems that affect engine performance and drivability. Recognizing these symptoms early can help prevent more serious issues and expensive repairs.
One of the most common signs of a bad camshaft position sensor is an illuminated check engine light. When the engine control module detects irregular signals from the sensor, it triggers this warning light and stores a diagnostic trouble code that can be read with a scanner.
Poor starting is another frequent symptom. The engine may crank normally but take longer to start or fail to start altogether. This happens because without proper camshaft position information, the ECM cannot correctly time fuel injection and ignition events necessary for starting.
Engine misfires and rough running often occur with a failing sensor. You might notice hesitation during acceleration, random misfiring, or an uneven idle. These symptoms result from improper fuel injection timing caused by inaccurate camshaft position data.
Stalling or unexpected engine shutdowns can happen when the sensor fails completely or provides intermittent signals. The engine might run normally then suddenly cut out without warning, creating potentially dangerous driving situations.
Decreased fuel economy often accompanies sensor issues because the ECM cannot optimize fuel delivery without accurate timing information. The computer typically defaults to a “rich” fuel mixture as a protective measure, consuming more fuel than necessary.
Camshaft Position Sensor Location
The camshaft position sensor is typically mounted on the cylinder head or timing cover, with its tip positioned near the camshaft gear or a dedicated reluctor wheel. The exact location varies significantly between different vehicle makes and models.
In many four-cylinder engines, you’ll find the sensor on the top or side of the cylinder head, often near the front of the engine. V6 and V8 engines might have multiple sensors, with one for each cylinder bank. Some designs place the sensor at the rear of the engine, making access more challenging.
Finding the sensor usually requires consulting the vehicle’s service manual for specific guidance. The sensor is typically connected to the engine wiring harness via a waterproof electrical connector and secured with one or two bolts.
Accessing the sensor for inspection or replacement sometimes requires removing other components like air intake ducts, decorative engine covers, or occasionally more substantial items like timing belt covers. The difficulty level of this task varies greatly depending on engine design and vehicle layout.
When looking for the camshaft position sensor, you’ll typically find a device with an electrical connector attached to a small cylindrical or rectangular housing. The sensor body may be black, gray, or another color depending on the manufacturer.
Here’s the second part of the comprehensive blog post about camshafts, continuing with the remaining 1600 words:
Camshaft Position Sensor Replacement Cost
The cost to replace a camshaft position sensor varies depending on several factors, including vehicle make and model, parts quality, and labor rates in your area. Understanding these costs helps you budget appropriately for this repair.
For most passenger vehicles, the sensor itself typically costs between $50 and $150 for an OEM-quality part. Aftermarket alternatives might cost less, while dealer-supplied original equipment could cost more. Luxury and high-performance vehicles generally have higher-priced sensors, sometimes exceeding $250 for the part alone.
Labor costs make up the remainder of the expense, typically ranging from $100 to $200 depending on sensor accessibility. Some vehicles allow quick and easy sensor replacement, requiring just 30 minutes of labor. Others might need several hours if the sensor is difficult to access or if multiple components must be removed first.
The total replacement cost usually falls between $150 and $350 for most common vehicles. However, this estimate can increase significantly for luxury or exotic cars, or in cases where the sensor is particularly difficult to access. Getting quotes from several repair shops can help you find the most reasonable price for your specific situation.
Some vehicle owners with mechanical knowledge choose to replace the sensor themselves to save on labor costs. This DIY approach can be practical for sensors with easy access, but challenging locations might require specialized tools or expertise that justify professional service.
How to Replace a Camshaft Position Sensor
Replacing a camshaft position sensor is a moderately difficult task that handy vehicle owners can often tackle themselves. This step-by-step guide covers the basic procedure, though specific details may vary by vehicle model.
Before beginning, gather the necessary tools: a socket set, screwdrivers, the replacement sensor, and possibly specialty tools depending on your vehicle. Ensure you have the correct sensor by checking your vehicle’s repair manual or matching part numbers.
Start by disconnecting the negative battery terminal to prevent electrical shorts or accidental system activation. This safety step is crucial when working with electronic components.
Locate the sensor using your repair manual as a guide. It’s typically mounted on the cylinder head or timing cover with an electrical connector attached. Some vehicles require removing engine covers, air intake components, or other obstructions to access the sensor.
Once you’ve reached the sensor, disconnect its electrical connector by pressing the release tab and gently pulling it apart. Take care not to damage the connector or wiring during this process.
Remove the mounting bolt or bolts securing the sensor to the engine using the appropriate socket or wrench. There are usually one or two fasteners holding it in place. Keep track of these fasteners as they may have a specific torque requirement for reinstallation.
Carefully extract the old sensor from its mounting hole. It might require gentle wiggling if it’s been in place for a long time. Note the orientation of the sensor before removal to ensure proper installation of the replacement.
Inspect the sensor mounting area for debris, oil residue, or damaged O-rings that could prevent proper sealing. Clean the area as needed and replace any damaged seals.
Install the new sensor in the same orientation as the original, ensuring it seats fully in its mounting hole. Replace and tighten the mounting bolts to the manufacturer’s specified torque. Over-tightening can damage the new sensor or its mounting threads.
Reconnect the electrical connector, making sure it clicks into place securely. Reattach any components removed for access, such as engine covers or intake ducts.
Finally, reconnect the battery and start the engine to verify proper operation. The check engine light should turn off after a few drive cycles if the sensor replacement has resolved the issue.
Camshaft Design and Performance Impact
The design of a camshaft significantly influences engine behavior and performance characteristics. Engineers carefully craft camshaft profiles to achieve specific power delivery, efficiency, and reliability goals.
Lobe profile is perhaps the most critical aspect of camshaft design. The shape of each lobe determines three key parameters: lift (how far the valve opens), duration (how long it stays open), and timing (when in the engine cycle the valve opens and closes). These parameters directly affect how an engine breathes and performs across different RPM ranges.
Higher lift allows more air and fuel to enter the combustion chamber, potentially increasing power. However, excessive lift can cause valve float at high RPM or accelerate valve train wear. Engine builders must balance lift with other mechanical limitations of the valve train.
Longer duration keeps valves open for more of the engine cycle, which typically shifts power production to higher RPM ranges. This characteristic is desirable for racing applications but often reduces low-end torque and fuel efficiency for street driving.
Lobe separation angle (LSA) refers to the spacing between intake and exhaust lobes on the camshaft. A narrower LSA typically produces more low-end torque and creates a choppy idle, while a wider LSA smooths idle quality and shifts power to higher RPM ranges.
Advanced camshaft designs incorporate features like asymmetrical lobes, which open valves quickly but close them more gradually to reduce valve train stress while maintaining performance benefits. Some performance camshafts also use different lobe profiles for intake and exhaust valves to optimize each for its specific function.
Camshaft Maintenance and Longevity
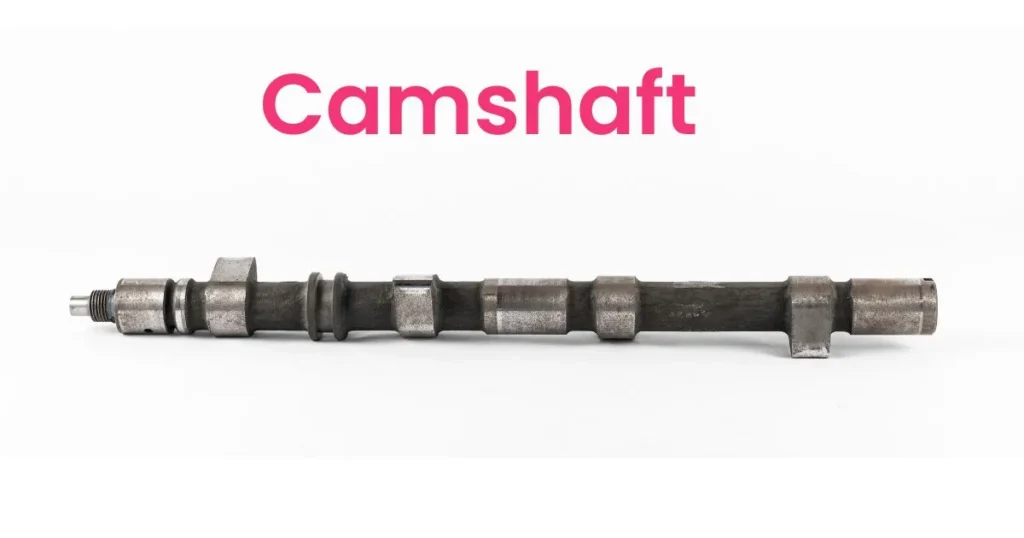
Proper maintenance can significantly extend camshaft life and prevent expensive engine repairs. Understanding how to care for this critical component helps ensure long-term reliability.
Regular oil changes with the manufacturer-recommended oil type and viscosity provide the most crucial protection for your camshaft. The oil film between the camshaft lobes and followers prevents metal-to-metal contact that would otherwise cause rapid wear. Most engine manufacturers suggest oil changes every 5,000 to 10,000 miles, though severe driving conditions may require more frequent service.
Engine warm-up practices also affect camshaft longevity. Allow your engine to reach operating temperature before high-RPM driving, especially in cold weather. Cold oil doesn’t flow properly through tiny clearances in the valve train, increasing wear during the critical first minutes of operation.
Timing belt or chain maintenance directly impacts camshaft health. These components synchronize the camshaft with the crankshaft, and their failure can lead to catastrophic engine damage in interference engines. Follow your vehicle’s maintenance schedule for timing component replacement, typically every 60,000 to 100,000 miles for timing belts.
Listen for unusual valve train noise, which might indicate camshaft problems. Ticking, clicking, or rattling sounds from the top of the engine could signal excessive lobe wear, collapsed lifters, or other valve train issues that require prompt attention.
Address check engine lights promptly, especially those related to camshaft position sensors or variable valve timing systems. Early intervention often prevents more extensive damage and keeps minor issues from developing into major repairs.
Common Camshaft Problems and Solutions
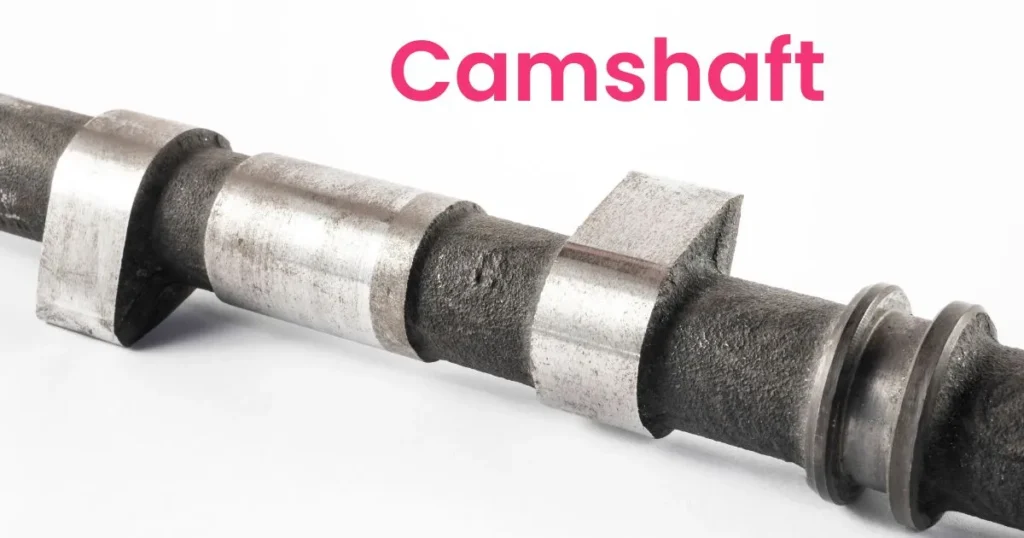
Camshafts can develop several common problems that affect engine performance. Knowing these issues and their solutions helps with diagnosis and repair decisions.
Camshaft wear appears as flattened lobes that no longer properly actuate the valves. This typically causes poor performance, rough idle, and reduced power. The solution usually requires camshaft replacement, along with new lifters or followers that may have been damaged by the worn camshaft.
Broken camshafts are less common but catastrophic when they occur. Excessive stress, manufacturing defects, or improper installation can cause the shaft to fracture. Symptoms include sudden power loss and severe engine noise. Replacement is the only solution, often requiring extensive disassembly and inspection for related damage.
Timing issues develop when the camshaft loses synchronization with the crankshaft due to a stretched timing chain, jumped timing belt, or failed tensioner. Symptoms include poor running, check engine lights, and potentially severe engine damage in interference engines. Proper timing component maintenance prevents most of these problems.
Lifter or follower failures often accompany camshaft problems. These components directly contact the camshaft lobes and can collapse, stick, or wear abnormally. Ticking noises, especially when the engine is cold, often signal lifter issues. Always replace these components when installing a new camshaft.
Oil-related problems frequently contribute to camshaft failures. Insufficient oil pressure, dirty oil, or extended oil change intervals reduce lubrication to critical surfaces. Maintaining proper oil level and quality helps prevent most oil-related camshaft damage.
FAQs About Camshafts
What happens if a camshaft position sensor fails completely?
A complete camshaft position sensor failure typically prevents the engine from starting or causes it to stall and not restart. The engine control module needs the timing information from this sensor to properly sequence fuel injection and ignition events, and without it, the engine cannot run properly.
Can I drive with a failing camshaft position sensor?
Driving with a failing camshaft position sensor is not recommended as it can cause unpredictable engine behavior, including stalling in traffic, which creates safety hazards. The inconsistent operation can also lead to catalytic converter damage from unburned fuel, resulting in much more expensive repairs.
How often should camshaft position sensors be replaced?
Camshaft position sensors don’t have a scheduled replacement interval and typically last 80,000 to 100,000 miles or more. They should be replaced when they show signs of failure or after diagnostic testing confirms they’re not functioning correctly.
What’s the difference between a camshaft and a crankshaft?
The camshaft controls valve operation through lobes that open and close valves, while the crankshaft converts the up-and-down motion of pistons into rotational force that drives the transmission and wheels. The camshaft typically rotates at half the speed of the crankshaft in four-stroke engines.
Do all engines have camshafts?
Most internal combustion engines use camshafts, but some designs like certain rotary engines and some experimental engines do not. Electric vehicles don’t have camshafts since they don’t use intake or exhaust valves, relying instead on electric motors for propulsion.
Can changing a camshaft improve fuel economy?
Yes, installing a camshaft with different specifications can improve fuel economy if it’s designed for efficiency rather than maximum power. Milder camshafts with appropriate lift and duration can enhance low-RPM torque and improve combustion efficiency, leading to better fuel economy during normal driving.