Shock absorbers are crucial components in a vehicle’s suspension system that help maintain optimal control, stability, and comfort during driving. These mechanical devices absorb and dampen the impact forces generated when a car traverses uneven surfaces, ensuring a smoother ride. By controlling the unwanted spring oscillations, shock absorbers prevent excessive bouncing and keep the tires firmly planted on the road surface, significantly enhancing safety and handling.
When driving over bumps or potholes, your vehicle’s springs compress and extend to absorb the impact. Without shock absorbers, these springs would continue to bounce, causing the car to shake uncontrollably. This continuous motion would make driving dangerous and uncomfortable. Shock absorbers convert this kinetic energy into heat energy through hydraulic fluid displacement, effectively dissipating the energy and stabilising the vehicle.
Understanding how shock absorbers function is essential for every vehicle owner, as they play a vital role in maintaining driving safety and comfort. This article explores the definition, working principles, various types, and essential parts of shock absorbers to provide comprehensive knowledge about these critical automotive components.
What is a Shock Absorber?
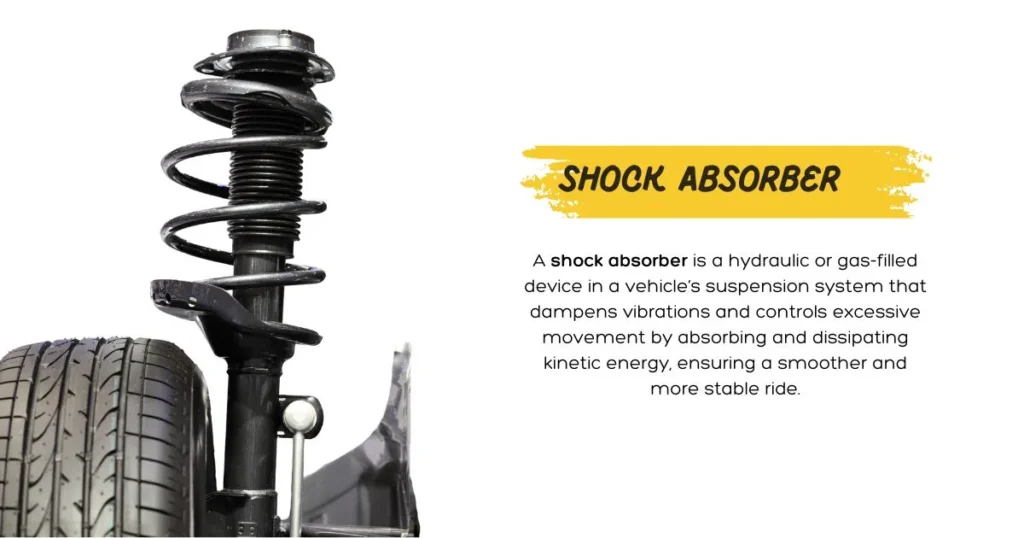
A shock absorber or damper is a mechanical or hydraulic device that absorbs and dampens vehicle shock impulses. It does this by converting the kinetic energy of suspension movement into heat energy that can dissipate through hydraulic fluid. Shock absorbers are velocity-sensitive dampening devices that resist the relative motion between a vehicle’s sprung (vehicle body) and unsprung (wheels and axles) masses.
Unlike the common misconception, shock absorbers don’t actually “absorb” shocks directly—that’s primarily the springs’ job in your suspension system. Instead, shock absorbers control how the springs move by dampening their oscillations. Without shock absorbers, your car would continue to bounce after hitting a bump until the spring’s energy naturally dissipated, which could take considerable time and distance.
Shock absorbers serve three primary functions in a vehicle: maintaining tire contact with the road, stabilizing the vehicle’s body movements, and providing comfortable ride quality. By controlling the rate at which suspension movement occurs, they ensure that your tires maintain consistent contact with the road surface, which is crucial for steering, braking, and overall vehicle control.
How Do Shock Absorbers Work?
Shock absorbers operate on the principle of fluid displacement to dampen spring oscillations. When your vehicle encounters a bump, the mechanical energy from the suspension movement is converted into heat energy through hydraulic fluid’s resistance passing through precisely calibrated orifices within the shock absorber.
Inside a typical hydraulic shock absorber, a piston moves within a cylinder filled with hydraulic oil. As the suspension moves, the piston pushes against the oil, forcing it through small holes or valves in the piston. This fluid flow restriction creates resistance, slowing the suspension’s movement. The resistance is proportional to the speed of the suspension movement—the faster the movement, the greater the resistance.
During compression (when the suspension compresses over a bump), the piston moves downward, forcing oil through the compression valve. During rebound (when the suspension extends after passing over a bump), the piston moves upward, forcing oil through the rebound valve. These valves are often designed to provide different resistance levels in each direction, allowing engineers to fine-tune the vehicle’s handling characteristics.
The heat generated during this process is dissipated through the shock absorber’s body into the surrounding air. Modern shock absorbers are designed with various features to enhance their performance, including gas pressurisation to prevent foaming of the hydraulic fluid and specialised valve designs to provide variable damping rates depending on conditions.
Parts of a Shock Absorber
Understanding the components of a shock absorber helps in appreciating its function and maintenance requirements. A typical shock absorber consists of several key parts working together to provide effective damping:
Piston and Piston Rod
The piston is a circular disc that moves up and down within the pressure tube. It contains precisely engineered valve systems that control the flow of hydraulic fluid during compression and rebound cycles. The piston rod connects the piston to the vehicle’s frame or body, transferring the movement from the suspension to the shock absorber mechanism.
The piston rod must be highly durable as it experiences significant forces during operation. It’s typically made from hardened steel and chrome-plated to resist corrosion and provide a smooth surface for the seal to slide against. The piston contains various orifices and spring-loaded valves that respond differently to varying pressure levels, allowing adaptive damping characteristics.
Pressure Tube and Reserve Tube
The pressure tube is the inner cylinder that contains the hydraulic fluid and houses the piston assembly. It’s designed to withstand high pressures generated during operation. In twin-tube shock absorbers, an outer reserve tube serves as a reservoir for excess hydraulic fluid and helps with heat dissipation.
The pressure tube must maintain perfect cylindrical geometry to ensure proper sealing and consistent performance. Any deformation or damage to this tube can lead to fluid leakage or inconsistent damping. The reserve tube in twin-tube designs provides additional fluid capacity and helps manage temperature fluctuations during operation.
Hydraulic Fluid
The hydraulic fluid is a specialized oil that flows through the shock absorber’s internal passages. Its viscosity and flow characteristics are crucial for proper damping performance. This fluid must maintain its properties across a wide temperature range and resist breakdown under the high pressures and temperatures experienced during operation.
Modern shock absorber fluids often contain additives to improve longevity, reduce foaming, and maintain consistent performance across various environmental conditions. The fluid’s resistance to flow through the valves and orifices creates the damping effect that controls suspension movement.
Seals and Bushings
Seals prevent the hydraulic fluid from leaking out of the shock absorber while keeping contaminants from entering. Bushings are used at the mounting points to allow for small movements and reduce noise transmission. These components are critical for maintaining the shock absorber’s performance and longevity.
High-quality seals must withstand the constant sliding motion against the piston rod without excessive wear. They must also maintain their sealing properties across a wide temperature range and resist degradation from exposure to the hydraulic fluid. Bushings are typically made from rubber or polyurethane compounds that provide the right balance of flexibility and durability.
Valving System
The valving system controls the flow of hydraulic fluid through the shock absorber. It consists of various discs, springs, and orifices that create resistance to fluid flow. Advanced shock absorbers feature sophisticated valving systems that provide different damping characteristics for driving conditions.
The valving system is often considered the heart of the shock absorber, as it determines the damping characteristics and overall performance. Engineers can tune these valves to provide specific handling characteristics for different vehicle applications, from comfortable cruising to high-performance driving.
Types of Shock Absorbers
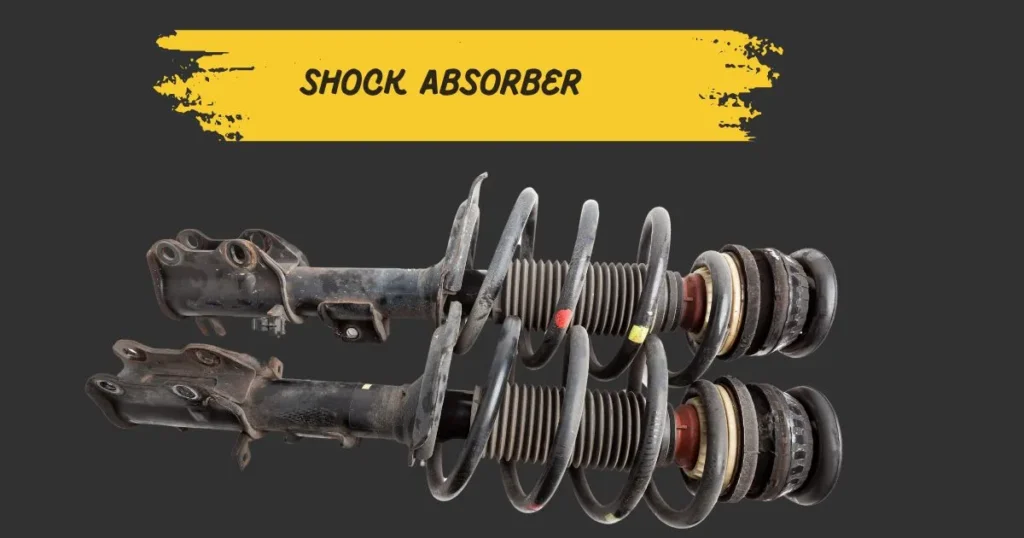
- Hydraulic type shock absorbers
- Gas-Charged Shock Absorbers
- Single acting shock absorber
- Double acting shock absorbers
- Friction type shock absorber
- Telescopic type shock absorber
- Strut Type Shock Absorbers
- Lever type shock absorber
Several types of shock absorbers are available, each with specific characteristics suited for different applications and vehicle types. Understanding these types can help in selecting the right shock absorbers for your vehicle’s needs:
1. Hydraulic Shock Absorbers
Hydraulic shock absorbers are the most common type used in vehicles today. They use hydraulic fluid to dampen suspension movement. When the piston moves within the cylinder, it forces the fluid through small orifices, creating resistance that slows the suspension movement.
These shock absorbers can be further classified into mono-tube and twin-tube designs. Mono-tube shocks have a single cylinder containing the piston and the hydraulic fluid, while twin-tube shocks have an inner working cylinder and an outer reserve tube. Hydraulic shock absorbers provide reliable performance and are cost-effective, making them popular in most passenger vehicles.
2. Gas-Charged Shock Absorbers
Gas-charged shock absorbers are an evolution of hydraulic ones, with the addition of pressurised nitrogen gas. The gas pressure helps prevent aeration or foaming of the hydraulic fluid, which can occur during rapid or extended operation of conventional hydraulic shock absorbers.
There are two main types of gas-charged shock absorbers: gas-pressurized twin-tube and high-pressure mono-tube designs. The gas-pressurized twin-tube version has a low-pressure nitrogen charge in the reserve tube, while the high-pressure mono-tube has a higher gas pressure in a separate chamber within the single tube. Gas-charged shock absorbers generally provide improved performance, especially in demanding driving conditions.
3. Single Acting Shock Absorbers
Single-acting shock absorbers provide damping in only one direction of movement—usually during the rebound phase when the suspension extends after compression. These were among the earliest types of shock absorbers and are rarely used in modern vehicles due to their limited functionality.
In a single acting shock absorber, the compression phase relies on the spring’s natural resistance, while the shock absorber’s hydraulic resistance controls the rebound phase. This design is more straightforward but less effective than double-acting shock absorbers, particularly for controlling the vehicle’s behavior during rapid suspension movements.
4. Double Acting Shock Absorbers
Double-acting shock absorbers dampen suspension movement in both the compression and rebound phases. By managing energy absorption in both directions of movement, they offer better control over the vehicle’s suspension.
Most modern vehicles use double acting shock absorbers because they provide superior handling and comfort characteristics. These shock absorbers have different valve arrangements for the compression and rebound strokes, allowing engineers to fine-tune the vehicle’s behavior in various driving conditions. The ability to independently control both compression and rebound movements is crucial for achieving optimal balance between ride comfort and handling performance.
5. Telescopic Shock Absorbers
Telescopic shock absorbers are the most common design in modern vehicles. They consist of a piston moving within a cylinder, with the entire assembly telescoping in and out as the suspension moves. This design allows for compact packaging and efficient operation.
Telescopic shock absorbers can be mounted in various orientations and configurations, making them versatile for different vehicle designs. They are available in mono-tube and twin-tube variations, as well as hydraulic and gas-charged designs. The telescopic design provides a good balance of performance, durability, and cost-effectiveness.
6. Strut Type Shock Absorbers
Strut-type shock absorbers combine the functions of traditional shock absorbers with structural support for the vehicle. In a strut assembly, the shock absorber is integrated with a coil spring to form a complete suspension unit that provides both dampening and support.
MacPherson struts are the most common type, where the shock absorber forms an integral part of the suspension system and serves as the upper pivot point for the steering. This design reduces the components needed and can provide better handling characteristics in some applications. Struts are commonly used in the front suspension of many front-wheel-drive vehicles.
7. Friction Type Shock Absorbers
Friction-type shock absorbers use mechanical friction between two surfaces to provide damping. These were among the earliest types of shock absorbers, consisting of discs or plates that rubbed against each other to create resistance to movement.
While largely obsolete in modern vehicles, friction shock absorbers were simple and inexpensive. However, they suffered from inconsistent performance as the friction surfaces wore down, and they couldn’t provide the variable damping rates needed for optimal vehicle control. Hydraulic and gas-charged shock absorbers in automotive applications have almost entirely replaced them.
8. Lever Type Shock Absorbers
Lever-type shock absorbers use a lever mechanism to amplify the suspension movement before it reaches the damping mechanism. They were common in older vehicles and some heavy-duty applications.
In a lever-type shock absorber, the suspension movement is transferred through a lever arm to the damping unit, which typically uses friction or hydraulic resistance. The lever mechanism allows for more significant mechanical advantage, which can be beneficial in specific applications. However, like friction-type shock absorbers, lever types have primarily been replaced by more advanced designs in modern vehicles.
Importance of Shock Absorbers in Vehicle Safety
Shock absorbers are crucial to vehicle safety by ensuring consistent tire contact with the road surface. This is essential for effective braking, steering, and overall vehicle control, especially during emergency maneuvers or when driving on uneven surfaces.
When shock absorbers wear out, they can significantly increase stopping distances and reduce steering precision. This is because worn shock absorbers cannot effectively control the vehicle’s weight transfer during braking and cornering, reducing traction and control. Studies have shown that cars with worn shock absorbers can experience up to 20% longer stopping distances than those with properly functioning shock absorbers.
Beyond braking performance, shock absorbers also contribute to stability during lane changes, cornering, and high-speed driving. They help prevent excessive body roll and maintain proper weight distribution across all four tires, which is crucial for maintaining control in dynamic driving situations. This is particularly important in emergencies where quick steering inputs are necessary to avoid obstacles.
Maintaining Shock Absorbers for Optimal Performance
Proper maintenance of shock absorbers is essential for ensuring your vehicle’s safety, comfort, and handling performance. While shock absorbers are designed to be durable, they do wear out over time and may require periodic inspection and replacement.
Signs of worn shock absorbers include excessive bouncing after hitting bumps, nose-diving during braking, squatting during acceleration, excessive body roll during cornering, and uneven tire wear patterns. If you notice any of these symptoms, it’s advisable to have your shock absorbers inspected by a qualified mechanic.
Most manufacturers recommend replacing shock absorbers every 50,000 to 100,000 miles, depending on driving conditions and vehicle type. However, this can vary significantly based on factors such as road conditions, driving style, and the quality of the shock absorbers installed. Regular inspection during routine maintenance can help identify worn shock absorbers before they significantly impact vehicle performance and safety.
How To Choose the Right Shock Absorbers for Your Vehicle?
Selecting the appropriate shock absorbers for your vehicle depends on several factors, including your driving style, typical road conditions, and performance expectations. Different shock absorbers are designed to prioritise either comfort, handling, or a balance between the two.
Standard replacement shock absorbers typically offer a similar ride quality to the original equipment, making them suitable for most drivers prioritising comfort and regular daily driving. On the other hand, performance-oriented shock absorbers often provide firmer damping for improved handling and reduced body roll, at the expense of some ride comfort.
Heavy-duty shock absorbers might be the best option for those who frequently drive on rough roads or use their vehicles for towing or hauling heavy loads. These provide increased durability and better control under demanding conditions. Adjustable shock absorbers offer the flexibility to modify damping characteristics according to changing needs, making them popular among enthusiasts who want to fine-tune their vehicle’s handling.
Frequently Asked Questions About
How do I know if my shock absorbers need replacement?
Signs of worn shock absorbers include excessive bouncing after hitting bumps, nose-diving during braking, poor handling around corners, uneven tire wear, and fluid leaks visible on the shock absorber body. If you notice these symptoms or if your vehicle has traveled more than 50,000 miles on the original shock absorbers, it’s advisable to have them inspected by a professional mechanic.
Can I replace shock absorbers myself?
While experienced DIY mechanics can replace shock absorbers, proper tools and knowledge are required. The process involves safely lifting the vehicle, removing wheels, and dealing with compressed springs that can cause injury if mishandled. Professional installation ensures proper alignment and torque specifications, which are crucial for safety and performance.
What’s the difference between shocks and struts?
Shock absorbers and struts dampen suspension movement, but struts also serve as structural components of the vehicle’s suspension system. Struts replace conventional suspension systems’ upper control arm and upper ball joint, forming a pivotal connection to the steering knuckle. Not all vehicles have struts; some use traditional shock absorbers with separate structural components.
How long do shock absorbers typically last?
The lifespan of shock absorbers varies depending on driving conditions, vehicle type, and quality of the components. On average, shock absorbers last between 50,000 and 100,000 miles. However, frequent driving on rough roads, heavy loads, or aggressive driving styles can significantly reduce their lifespan. Regular inspection is the best way to determine when replacement is necessary.
Can I mix different types of shock absorbers on my vehicle?
Mixing different types or brands of shock absorbers on the exact vehicle is generally not recommended. Using different shock absorbers can lead to uneven handling characteristics and potentially dangerous driving conditions. When replacing shock absorbers, it’s best to replace them in pairs (front or rear) with identical units to maintain balanced vehicle dynamics.
Do shock absorbers affect fuel efficiency?
Yes, shock absorbers can indirectly affect fuel efficiency. Worn shock absorbers cause excessive bouncing and oscillation, which reduces tire contact with the road. This can increase rolling resistance and make the engine work harder to maintain speed, resulting in higher fuel consumption. Properly functioning shock absorbers help maintain optimal tire contact and vehicle aerodynamics, improving fuel efficiency.