Springs are fundamental mechanical components that store and release energy through their elastic deformation. When you press or pull a spring, it absorbs energy and returns to its original shape when the force is removed. This simple yet ingenious mechanism makes springs essential in countless applications from everyday items to complex machinery.
Springs have been used for centuries, evolving from primitive wooden designs to the sophisticated metal and composite springs we use today. Their ability to store potential energy and convert it to kinetic energy makes them invaluable in mechanical systems worldwide.
Whether you’re driving a car, writing with a pen, or sitting on a chair, springs are likely working silently to improve your experience. These versatile devices come in various shapes, sizes, and materials, each designed for specific applications and performance requirements.
In this comprehensive guide, we’ll explore what springs are, their various types, how they work, and their wide-ranging applications across industries. We’ll also discuss the advantages and limitations of springs to help you understand why these simple mechanical devices remain irreplaceable in modern engineering.
What Is A Spring and It’s Mechanical Function
Springs are elastic objects that store mechanical energy when compressed, stretched, or twisted. They return to their original shape once the force is removed, releasing the stored energy. This energy-storing capability makes springs essential components in mechanical systems.
The elasticity of springs comes from the material’s ability to deform temporarily without permanent damage. Most springs are made from materials with high yield strength, allowing them to stretch or compress significantly before experiencing permanent deformation.
The fundamental principle behind spring operation is Hooke’s Law, which states that the force needed to extend or compress a spring is proportional to the distance it is stretched or compressed. This is expressed mathematically as F = kx, where F is the force, k is the spring constant (a measure of stiffness), and x is the displacement from the spring’s resting position.
Springs work by converting energy between potential and kinetic forms. When you compress a spring, you’re adding potential energy to it. When you release it, that potential energy converts to kinetic energy as the spring returns to its natural state.
The function of a spring in mechanical systems varies widely. In some cases, springs provide force or torque, while in others, they absorb shock, maintain contact between components, or store and release energy in controlled ways.
Spring performance is characterized by several key parameters including spring rate (stiffness), free length, solid height, maximum load capacity, and fatigue life. Engineers select springs based on these parameters to match specific application requirements.
Materials commonly used for springs include various steel alloys, particularly spring steel, which offers excellent elasticity and fatigue resistance. Other materials include beryllium copper, phosphor bronze, titanium, and even rubber or plastic for specialized applications.
Types of Springs
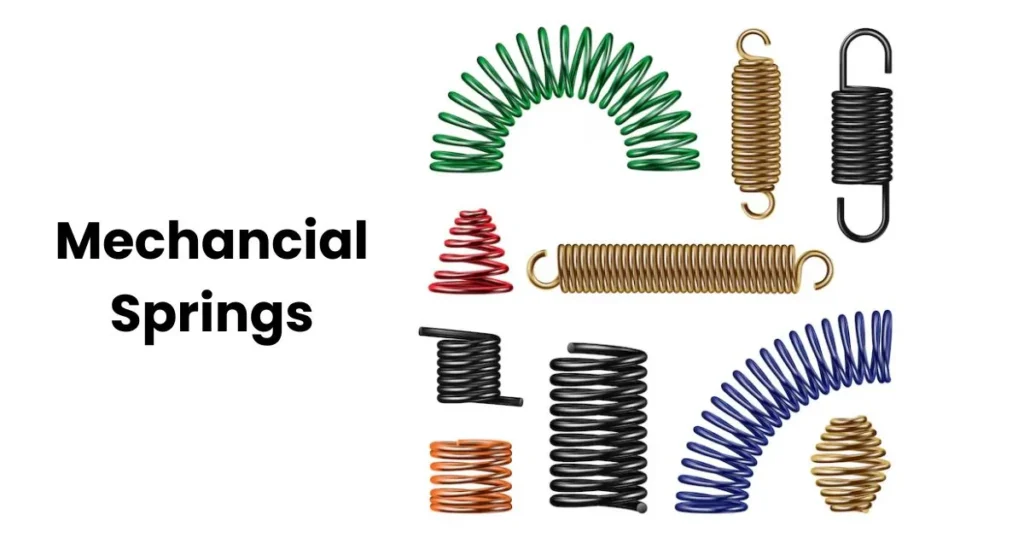
- Extension Springs
- Compression Springs
- Constant Force Springs
- Torsion Springs
- Belleville Springs
- Volute Springs
- Flat Springs
- Garter Springs
- Drawbar Springs
- Gas Springs
1. Extension Springs
Extension springs, also called tension springs, are tightly wound coils designed to operate with a pulling force. Unlike compression springs, they’re manufactured with a built-in initial tension that keeps the coils tightly together.
These springs work by stretching when a load is applied to the hooks, loops, or eyes at their ends. They resist this stretching force and try to pull back to their original position, creating tension.
Extension springs typically have hooks or loops at both ends for attachment to the components they connect. These end configurations come in various styles, including machine loops, crossover loops, extended hooks, and side hooks.
You’ll find extension springs in trampolines, garage doors, toys, farm machinery, and many other applications where components need to be pulled together or where counterbalance forces are required.
The initial tension in extension springs is an important design feature that keeps the coils closed in the unloaded position. This tension can be adjusted during manufacturing to meet specific application requirements.
2. Compression Springs
Compression springs are open-coiled springs designed to resist compressive forces. They push back when squeezed, making them perfect for applications requiring resistance against pressure.
These cylindrical springs are typically made from round wire wound into a helix with constant pitch. When force is applied, the coils compress closer together, storing energy that’s released when the force is removed.
Compression springs are found everywhere—from ballpoint pens and mattresses to automotive suspension systems and industrial machinery. Their simple design and reliable performance make them the most widely used spring type.
Manufacturing techniques for compression springs include cold winding for smaller springs and hot winding for larger, heavier-duty applications. The ends can be closed and ground, closed but unground, or open, depending on the specific application requirements.
Compression springs can be designed with variable pitch or variable diameter to provide progressive spring rates, meaning the spring becomes stiffer as it compresses further. This feature is particularly useful in vehicle suspensions.
3. Constant Force Springs
Constant force springs are a unique category that provides nearly constant resistance over their extension range. Unlike conventional springs where force increases with displacement, these springs deliver consistent force throughout their movement.
These springs are typically made from pre-stressed, flat strip material wound tightly around itself or a drum. When extended, the material naturally wants to return to its tightly wound state, creating a nearly constant pulling force.
The flat strip design of constant force springs makes them compact when retracted but capable of extending to significant lengths. This space-saving characteristic makes them valuable in applications with size constraints.
Constant force springs are commonly used in retractable devices like tape measures, cord reels, counterbalance systems, and medical equipment. Their predictable, even tension makes them ideal for applications requiring controlled, smooth movement.
Manufacturing constant force springs requires precision forming and heat treatment to achieve the desired constant force characteristics. The material must be carefully selected and processed to maintain consistent performance over many cycles.
4. Torsion Springs
Torsion springs operate by twisting or rotating along their axis, storing energy through angular deflection. When torque is applied, the spring’s legs rotate through an angle, creating resistance that increases proportionally with the angle of twist.
Unlike compression and extension springs that work along a linear axis, torsion springs work rotationally. This makes them ideal for applications requiring rotational force or torque.
Torsion springs typically feature straight legs extending from a coiled body. These legs transmit the torque and serve as attachment points. The ends can be formed into various shapes to suit specific mounting requirements.
Common applications for torsion springs include clothespins, door hinges, clipboards, counterbalance systems, and many mechanical devices requiring rotational resistance or return-to-position functionality.
The torque produced by a torsion spring is determined by its wire size, coil diameter, number of coils, and material properties. Engineers adjust these parameters to achieve the desired rotational resistance.
5. Belleville Springs
Belleville springs, also called Belleville washers or disc springs, are conical-shaped discs that flatten when loaded and return to their original shape when unloaded. Their unique geometry allows them to support heavy loads despite their compact size.
These springs can be stacked in various configurations to modify their force-deflection characteristics. Stacking them in the same direction increases the load capacity, while stacking them in alternating directions increases the deflection range.
Belleville springs excel in applications with severe space limitations that require high spring forces. Their compact design makes them ideal for bolt assemblies, valves, clutches, and other applications where space is at a premium.
The conical shape of Belleville springs provides a non-linear spring rate, meaning the force does not increase proportionally with deflection. This characteristic can be advantageous in applications requiring specialized force profiles.
Manufacturers can modify the force-deflection characteristics of Belleville springs by adjusting their thickness, diameter, height, and material. This flexibility allows engineers to fine-tune these springs for specific application requirements.
6. Volute Springs
Volute springs are conical-shaped compression springs made from flat strip material wound into a spiral form. Their unique geometry provides increasingly greater resistance as they compress, resulting in a variable spring rate.
The conical design of volute springs allows them to collapse into a very compact space when fully compressed. This space-saving feature makes them valuable in applications with severe height limitations.
Volute springs excel in high-shock applications due to their ability to absorb significant energy before reaching solid height. This makes them ideal for use in heavy machinery, automotive suspensions, and impact-absorption systems.
Unlike conventional coil springs, volute springs distribute stress more evenly throughout their structure. This stress distribution helps prevent premature failure and extends the spring’s service life in demanding applications.
Manufacturing volute springs requires specialized equipment to form the flat material into the precise conical spiral shape. The material must have excellent fatigue resistance to withstand the repeated compression and expansion cycles.
7. Flat Springs
Flat springs are made from flat sheets or strips of metal formed to store and release energy when deflected. Unlike coil springs, they rely on the bending or flexing of the material rather than coiling for their spring action.
These springs come in countless shapes and designs, from simple leaf springs to complex stamped forms. The versatility of flat springs allows engineers to create custom solutions for unique application requirements.
Flat springs are commonly used in electronic devices, locks, switches, and medical instruments. Their compact design makes them ideal for applications where space is limited but reliable spring action is required.
Manufacturing flat springs typically involves stamping or cutting processes followed by forming operations to create the desired shape. Heat treatment is often applied to enhance the spring’s mechanical properties and performance.
The performance of flat springs depends on factors such as material thickness, width, length, and shape. Engineers manipulate these parameters to achieve the desired spring characteristics for specific applications.
8. Garter Springs
Garter springs are essentially extension springs with their ends connected to form a continuous circle. This circular configuration creates a spring that applies uniform radial pressure around its circumference.
These springs function by expanding when subjected to internal pressure and contracting when external forces are applied. The continuous coil design ensures even force distribution throughout the entire spring.
Garter springs are widely used in sealing applications, such as oil seals, shaft seals, and piston rings. Their ability to maintain consistent radial tension makes them ideal for creating effective seals between moving components.
The design of garter springs allows them to accommodate minor misalignments while maintaining their sealing effectiveness. This flexibility is particularly valuable in applications where perfect alignment is difficult to achieve.
Manufacturers can adjust the wire diameter, coil diameter, and number of coils to tailor garter springs for specific applications. These modifications allow engineers to achieve the precise radial tension required for optimal performance.
9. Drawbar Springs
Drawbar springs are specialized compression springs designed for applications requiring significant force control. They’re often used in mechanical systems where precise tension or pulling force is needed over extended distances.
These springs typically feature a heavy-duty design with closely wound coils that provide reliable performance under demanding conditions. The robust construction ensures longevity even when subjected to frequent cycling and high loads.
Drawbar springs are commonly found in industrial machinery, railway coupling systems, and heavy equipment. They help manage the forces between connected components while absorbing shock and vibration during operation.
The design of drawbar springs allows them to handle substantial tension loads while maintaining proper alignment between the connected components. This makes them ideal for applications where misalignment could cause system failure or reduced efficiency.
Engineers select drawbar springs based on their load capacity, deflection characteristics, and fatigue resistance. These parameters ensure the spring performs reliably throughout its intended service life in challenging operating environments.
10. Gas Springs
Gas springs, also called gas struts or gas shocks, use compressed gas (typically nitrogen) enclosed in a cylinder with a piston to provide force. They operate on the principle that gas pressure increases when compressed and decreases when expanded.
Unlike mechanical springs, gas springs provide damping along with spring force. This combined action allows them to control the speed of movement, making them ideal for controlled opening and closing applications.
Gas springs are commonly used in automotive hatchbacks, office chairs, medical equipment, and industrial machinery. Their ability to provide controlled motion and hold objects in position makes them highly versatile.
The force produced by gas springs can be adjusted by changing the gas pressure during manufacturing. This adjustability allows engineers to precisely match the spring force to application requirements.
Modern gas springs often include features like locking mechanisms, adjustable damping, and temperature compensation. These enhancements expand their functionality and make them suitable for increasingly sophisticated applications.
11. Air Springs
Air springs are pneumatic devices that use compressed air contained within a flexible bellows to support loads and absorb shock. They provide adjustable spring rates by simply changing the air pressure inside the bellows.
Unlike conventional metal springs, air springs offer variable stiffness without changing components. This adjustability makes them ideal for applications where load conditions change frequently or where leveling is required.
Air springs are extensively used in vehicle suspension systems, particularly in heavy trucks, buses, and luxury vehicles. They’re also found in industrial equipment, railway systems, and vibration isolation platforms.
The design of air springs typically features a rubber bellows reinforced with cords or fabric to withstand internal pressure. This construction allows for significant compression and extension while maintaining strength and durability.
Advanced air spring systems often include electronic controls that automatically adjust air pressure based on load conditions and road surfaces. This intelligent adaptation optimizes ride comfort and handling characteristics in real-time.
Applications of Springs Across Industries
Springs play crucial roles across virtually all industries, from automotive and aerospace to consumer products and medical devices. Their versatility makes them indispensable components in countless mechanical systems.
In the automotive industry, springs are fundamental to suspension systems, valve trains, clutches, and brakes. They help absorb road shock, control engine valves, transfer power, and stop vehicles safely and efficiently.
The aerospace sector relies on springs for landing gear, control surfaces, and various mechanical systems. These applications demand springs with exceptional reliability, precise performance, and minimal weight.
Consumer products incorporate springs in countless ways—from mattresses and furniture to toys and tools. The familiar “click” of a pen or the resistance in a stapler comes from carefully designed spring mechanisms.
Industrial machinery uses springs for everything from safety valves and conveyor systems to manufacturing equipment and power tools. These applications often require springs capable of withstanding harsh operating conditions.
Medical devices frequently incorporate springs in surgical instruments, hospital beds, and diagnostic equipment. These applications demand springs made from biocompatible materials with precise performance characteristics.
Electronics rely on contact springs, switch springs, and battery contacts. These tiny but essential components ensure reliable electrical connections in devices we use every day.
Advantages of Springs in Mechanical Systems
Springs offer numerous advantages that make them indispensable in mechanical design. Their ability to store and release energy efficiently provides the foundation for countless mechanical processes.
One key advantage is their simplicity—springs are uncomplicated components that perform reliably with minimal maintenance. This simplicity translates to lower manufacturing costs and reduced maintenance requirements.
Springs excel at absorbing shock and vibration, protecting other components from damage. This capability extends the service life of mechanical systems and improves overall reliability.
The versatility of springs allows engineers to address diverse mechanical challenges with a single component type. By adjusting parameters like wire diameter, coil diameter, and material, springs can be tailored for specific applications.
Springs provide consistent performance over long periods when properly designed and manufactured. This reliability makes them suitable for critical applications where failure could have serious consequences.
Modern manufacturing techniques allow for precise control of spring characteristics, ensuring consistent performance across production batches. This consistency is essential for applications requiring interchangeable components.
Disadvantages of Springs to Consider
Despite their many advantages, springs have certain limitations that engineers must consider. Understanding these drawbacks helps in making informed decisions about spring selection and application.
Springs can experience fatigue failure after repeated cycling, especially under high stress conditions. This fatigue occurs as microscopic cracks develop and propagate through the material, eventually leading to complete failure.
Temperature changes affect spring performance by altering the material properties. Most springs lose some of their elasticity at high temperatures and may become brittle at extremely low temperatures, limiting their operating range.
Many spring materials are susceptible to corrosion in harsh environments. This vulnerability can lead to premature failure unless appropriate materials or protective coatings are selected for the specific operating conditions.
Springs typically exhibit some degree of permanent set over time, meaning they don’t completely return to their original dimensions after extended use. This loss of elasticity can affect system performance and may require periodic replacement.
Designing springs for specific applications requires careful engineering analysis. Incorrect selection or improper installation can lead to inadequate performance or premature failure, potentially causing system-wide issues.
Spring Materials and Manufacturing Methods
The performance of a spring largely depends on its material. Spring steel is the most common material due to its excellent combination of strength, elasticity, and fatigue resistance at a reasonable cost.
High-carbon steel (music wire) is widely used for small to medium-sized springs requiring high tensile strength. This material offers good fatigue resistance and maintains its elastic properties even after repeated cycling.
Stainless steel springs resist corrosion, making them ideal for applications exposed to moisture or chemicals. Common grades include 302, 304, and 316, each offering different combinations of strength and corrosion resistance.
Phosphor bronze and beryllium copper springs are used in applications requiring good electrical conductivity along with spring properties. These alloys also offer better corrosion resistance than standard carbon steels.
For high-temperature applications, springs made from nickel alloys like Inconel or Nimonic maintain their elastic properties at temperatures that would cause conventional steel springs to fail.
Manufacturing methods vary based on spring type and production volume. Cold winding is common for small to medium springs, while hot winding is used for larger springs with heavier wire diameters.
Advanced manufacturing techniques like CNC coiling allow for precise control of wire feed, mandrel speed, and pitch, resulting in springs with highly consistent properties. This precision is crucial for applications with stringent performance requirements.
Spring Design Parameters and Calculations
Designing a spring involves balancing several key parameters to achieve the desired performance. These include wire diameter, coil diameter, free length, solid height, spring rate, and material selection.
Spring rate (stiffness) is a fundamental characteristic that describes how much force is needed to compress or extend a spring a given distance. It’s calculated using formulas that account for material properties and spring geometry.
For compression springs, engineers calculate parameters like the solid height (when all coils are touching) and buckling potential. These calculations ensure the spring performs properly within its intended application constraints.
Extension springs require analysis of initial tension and hook or loop strength. These calculations help prevent failures at the connection points, which are often the weakest part of extension spring assemblies.
Torsion spring calculations focus on torque capacity and angular deflection. Engineers must ensure the spring can provide the required torque without exceeding material stress limits.
Fatigue life predictions are essential for applications where springs undergo many cycles. These calculations consider factors like mean stress, stress amplitude, material properties, and surface conditions.
Computer-aided design software has revolutionized spring design by allowing engineers to simulate performance under various conditions. These tools help optimize designs before physical prototypes are manufactured.
Springs in Automotive Suspension Systems
Springs are fundamental components in vehicle suspension systems, where they support the vehicle weight and absorb road shock. This dual role is crucial for both ride comfort and handling performance.
Coil springs are the most common type used in modern vehicle suspensions. They provide a good balance of performance, cost, and packaging efficiency, making them suitable for most passenger vehicles.
Leaf springs, made from stacked flat steel plates, are often used in heavy vehicles like trucks and SUVs. Their design allows them to support heavy loads while also functioning as locating links in the suspension geometry.
Air springs provide adjustable ride height and spring rate, benefits that make them popular in luxury vehicles and heavy commercial vehicles. By simply changing air pressure, these systems can adapt to different loads and road conditions.
Torsion bar springs, which operate by twisting along their axis, were common in older vehicle designs. Though less common today, they still appear in specific applications where their compact packaging offers advantages.
Modern suspension systems often combine springs with hydraulic or gas-filled shock absorbers. This combination allows the spring to support the vehicle weight while the shock absorber controls oscillation and improves ride quality.
Advanced suspension systems incorporate electronically controlled springs or air springs that adjust automatically based on road conditions, vehicle speed, and driver preferences. These adaptive systems optimize the balance between comfort and handling.
Spring Maintenance and Troubleshooting
Proper maintenance extends spring life and ensures consistent performance. Regular inspection for signs of wear, corrosion, or deformation helps identify potential issues before failure occurs.
Signs of spring failure include reduced height (sagging), cracking, permanent deformation, or corrosion. Any of these conditions indicates the spring may need replacement to maintain system performance.
In automotive applications, sagging springs lead to reduced vehicle height, altered suspension geometry, and compromised handling. Regular inspection of ride height can help identify spring fatigue before it affects safety.
Industrial springs should be inspected according to manufacturer recommendations or industry standards. This inspection often includes measuring free length, checking for cracks, and assessing surface condition.
When replacing springs, it’s crucial to use components with identical specifications to the original. Substituting a spring with different characteristics can lead to system imbalance or premature failure of other components.
Proper lubrication is essential for springs that operate in sliding contact with other components. The correct lubricant reduces friction and wear while protecting against corrosion in challenging environments.
FAQs About Springs
What is the main function of a spring in mechanical systems?
A spring stores mechanical energy when deformed and releases this energy when returning to its original shape. This energy storage and release mechanism allows springs to absorb shock, provide force, maintain contact between components, and control movement in mechanical systems.
How do I choose the right spring for my application?
Select the right spring by first determining the required force, deflection range, and space constraints. Then consider the operating environment, including temperature range and exposure to corrosive elements. Finally, evaluate fatigue requirements based on the expected number of cycles during the component’s service life.
Can springs wear out or fail over time?
Yes, springs can fail due to fatigue, corrosion, or overloading. Fatigue occurs after repeated cycling, especially under high stress. Corrosion weakens the material structure, while overloading causes immediate deformation or breakage. Regular inspection and proper selection for the operating conditions help prevent premature failure.
Why are different materials used for making springs?
Different spring materials offer varying combinations of strength, elasticity, temperature resistance, and corrosion resistance. Steel alloys provide excellent strength and elasticity for most applications, while stainless steel offers corrosion resistance. Exotic alloys serve in extreme temperatures, and non-metallic materials provide unique properties for specialized applications.
How do temperature changes affect spring performance?
Temperature significantly impacts spring performance by altering material properties. High temperatures reduce elasticity and can lead to relaxation or set, while extremely low temperatures may cause brittleness in some materials. Springs designed for extreme temperature environments use special alloys that maintain their properties across the required temperature range.
What’s the difference between linear and progressive springs?
Linear springs provide consistent force increase per unit of deflection throughout their range, following Hooke’s Law precisely. Progressive springs, by contrast, increase in stiffness as they compress, providing a variable spring rate. This progressive behavior is achieved through variable coil spacing, conical shapes, or material thickness variations.